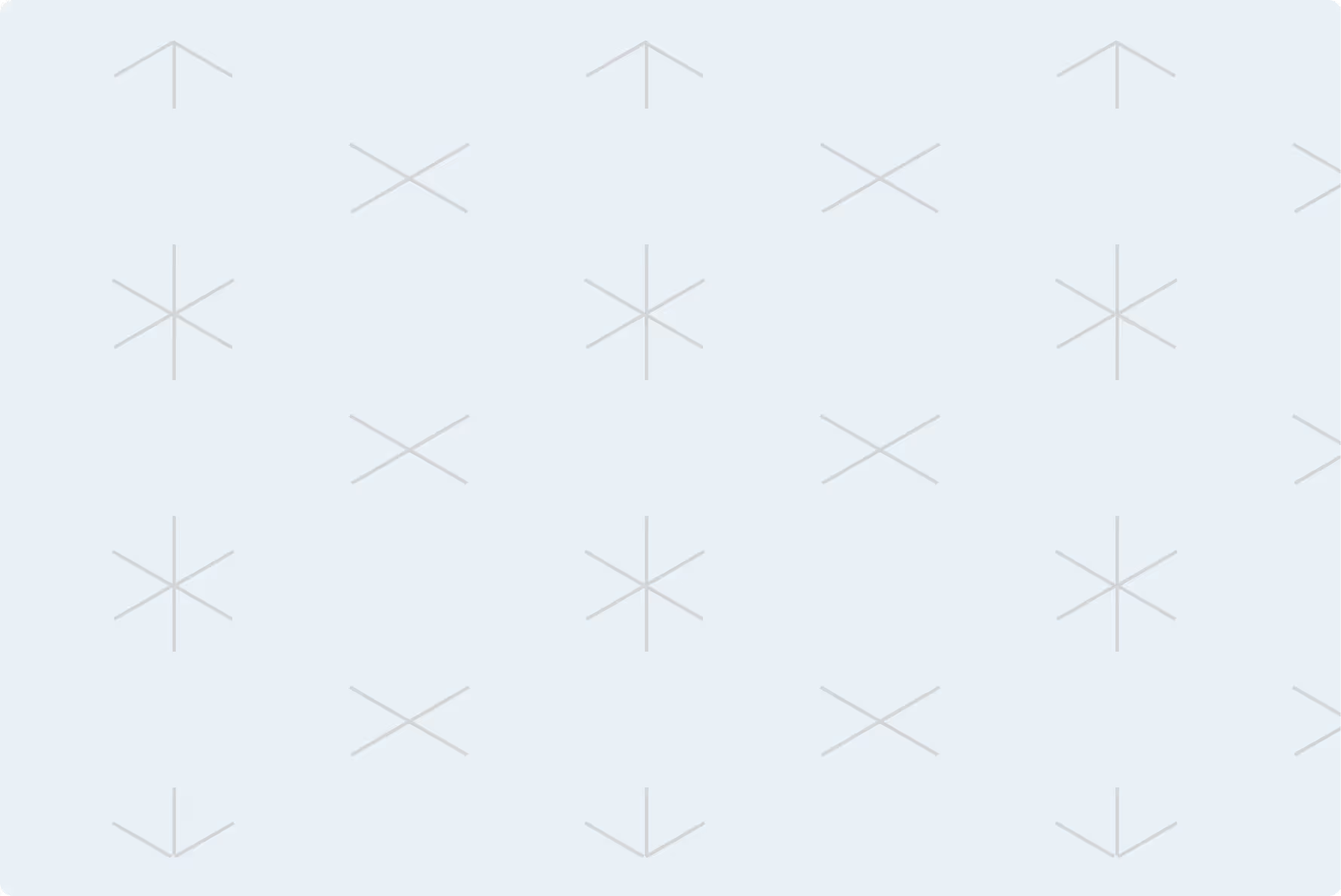
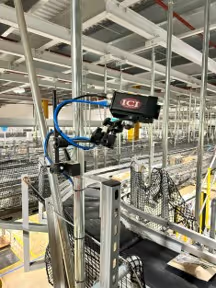
A global online retailer implemented MultiSensor AI to monitor its High Speed Gapper Beds—critical assets in the material handling process. Real-time thermal monitoring led to early detection of belt tension issues, MultiSensor AI reduced downtime by 30%, increased throughput 11.4x, and cut maintenance costs by 40%, delivering a 20x return on investment.
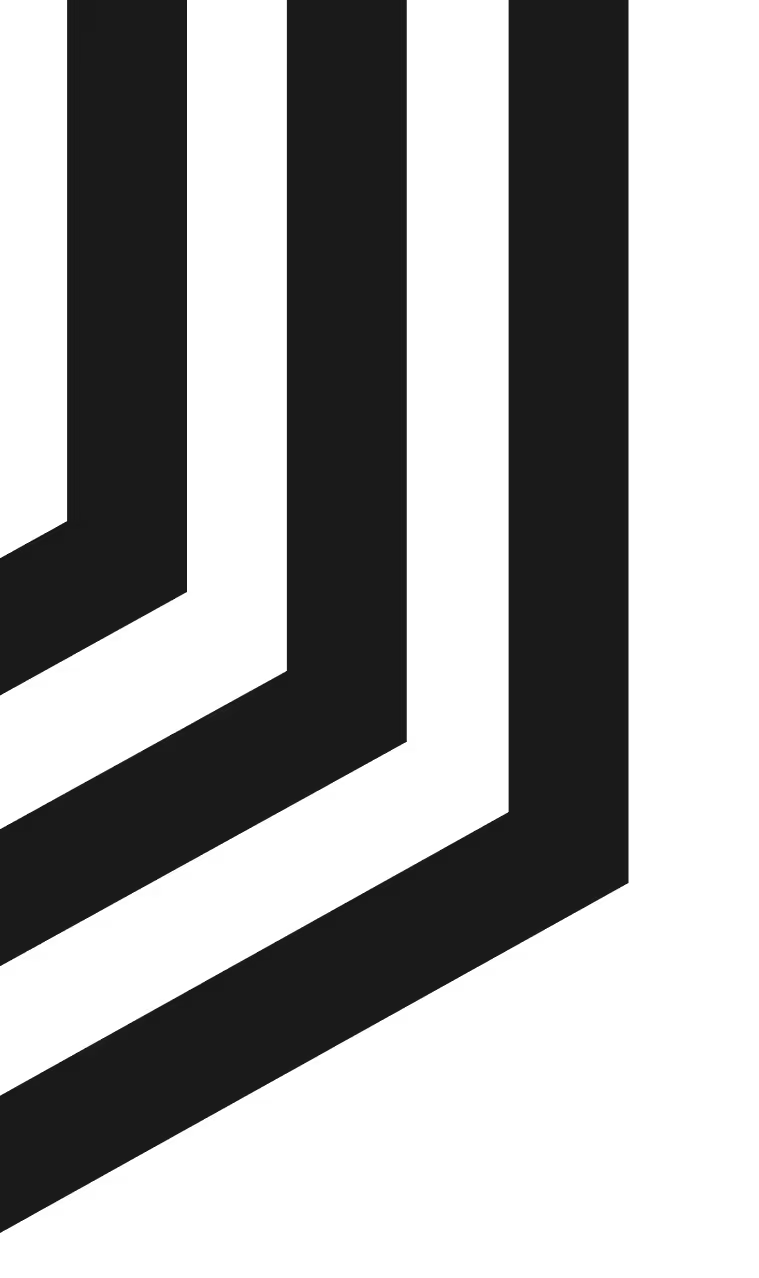
High Speed Gapper Beds are a vital component in the retailer’s logistics chain with very high throughput. As a single point of failure, any malfunction leads to downstream disruption and lost productivity. Prior to MultiSensor AI, these beds were monitored manually with no real-time alert system—making it difficult to catch issues like belt over-tensioning or mechanical defects before failure. Failures could escalate quickly—sometimes within hours—leading to costly downtime and emergency maintenance.
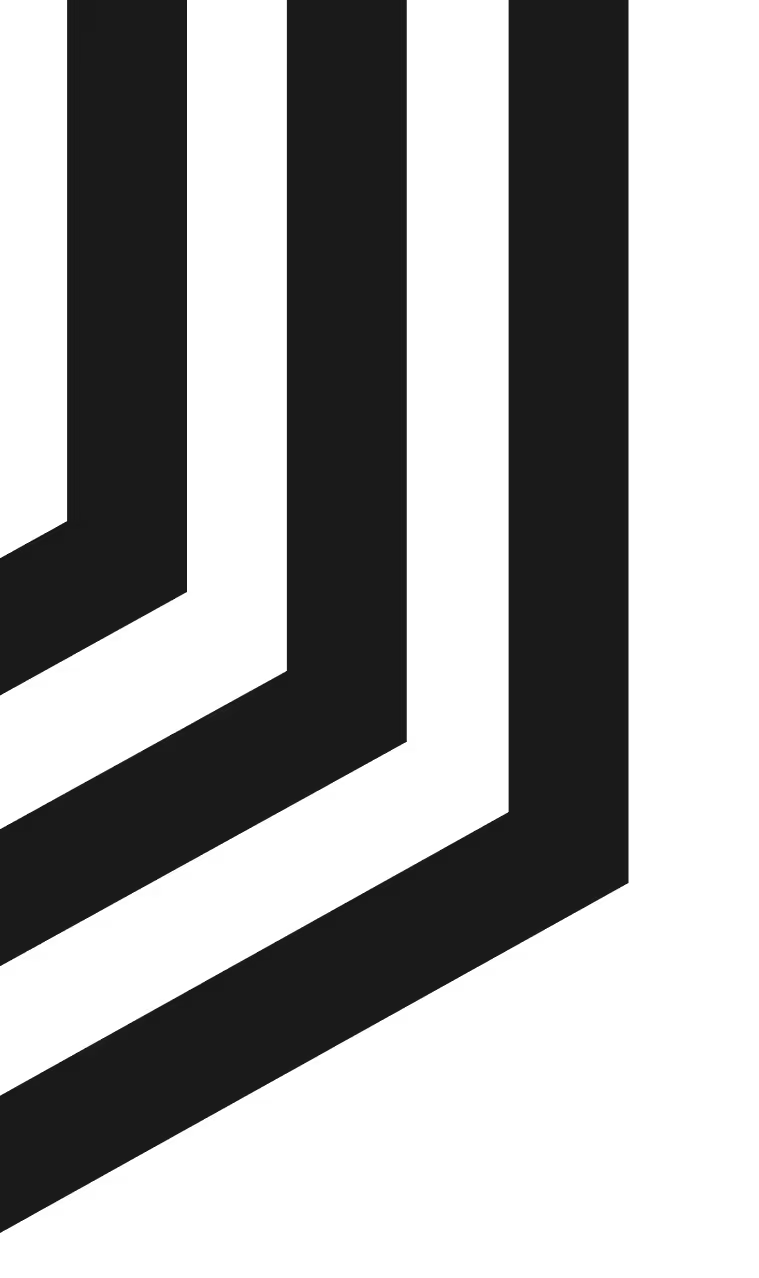
MultiSensor AI deployed fixed thermal monitoring points directly on the High Speed Gapper Beds. These sensors provided live data on belt temperature and tension. The system continuously analyzed this data, allowing the Reliability Maintenance Engineering (RME) team to identify over-tensioned belts and intervene before failures occurred. This real-time monitoring eliminated the need for frequent manual inspections and enabled more efficient, targeted maintenance.
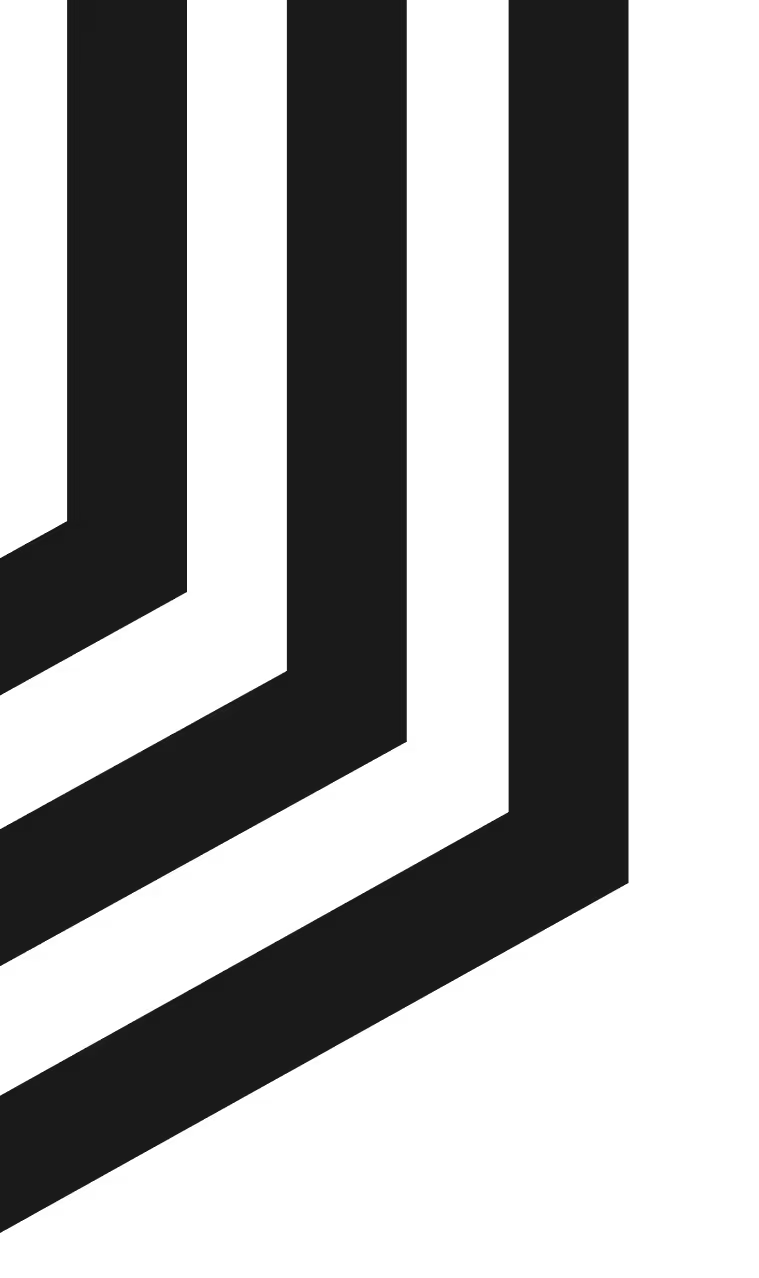
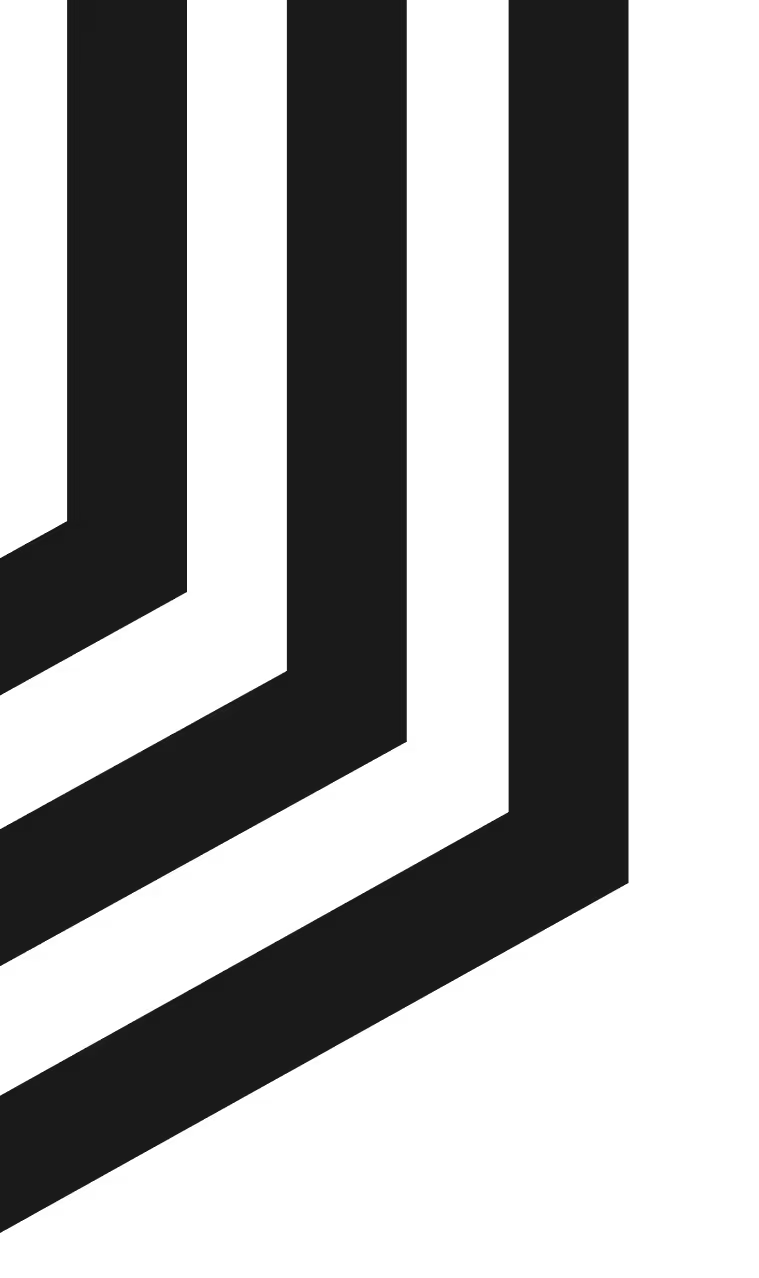
- 30% reduction in downtime through early detection of belt tension issues
- 11.4x increase in throughput from optimized gapping bed performance
- 40% maintenance cost savings by minimizing reactive repairs and spare part usage
- 20x return on investment driven by operational gains and cost reductions
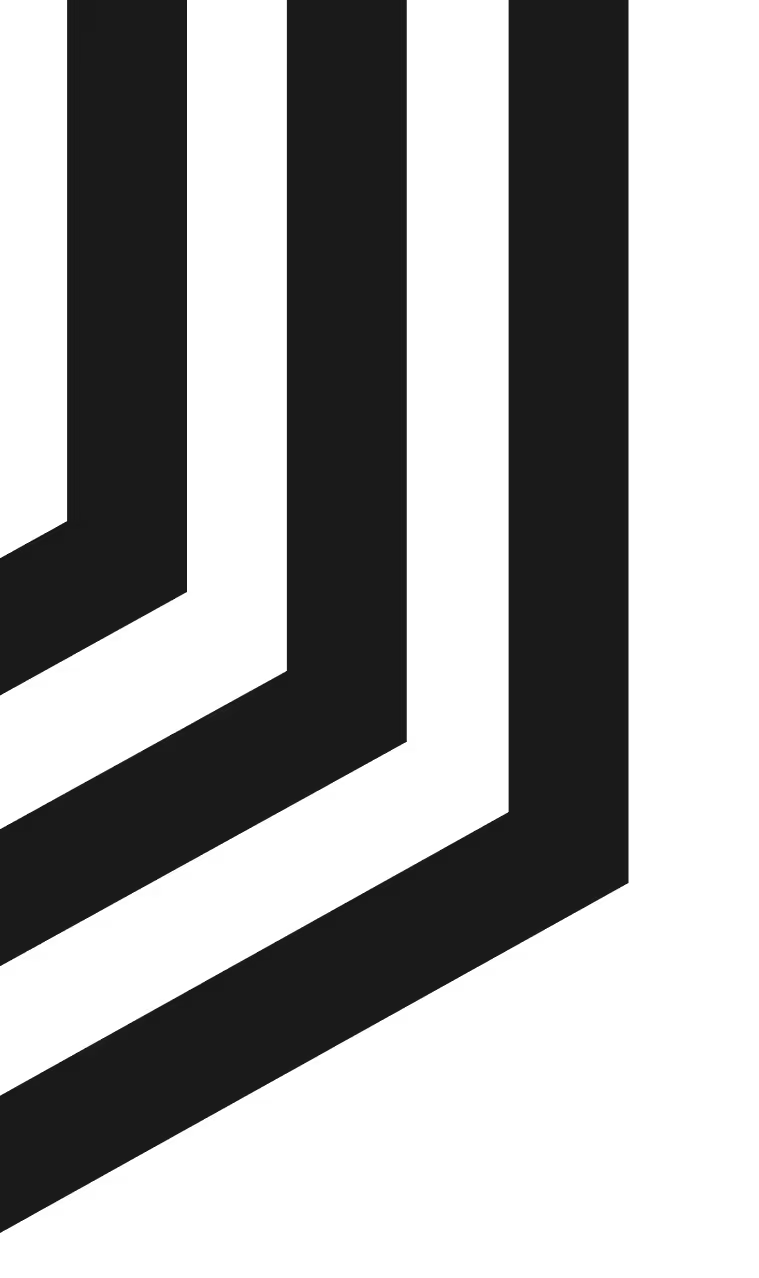
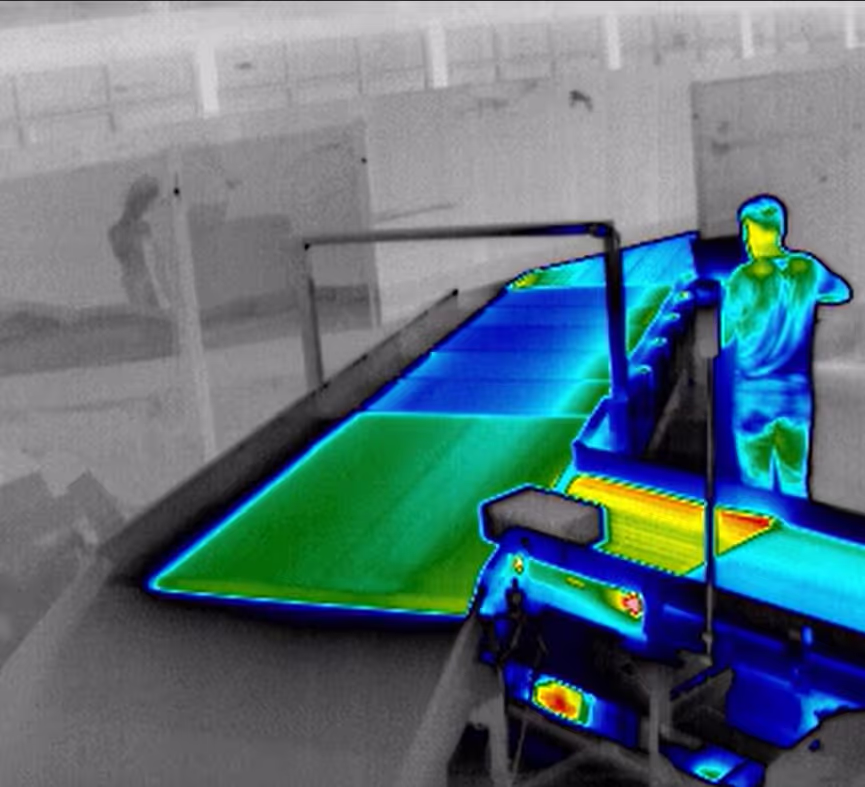
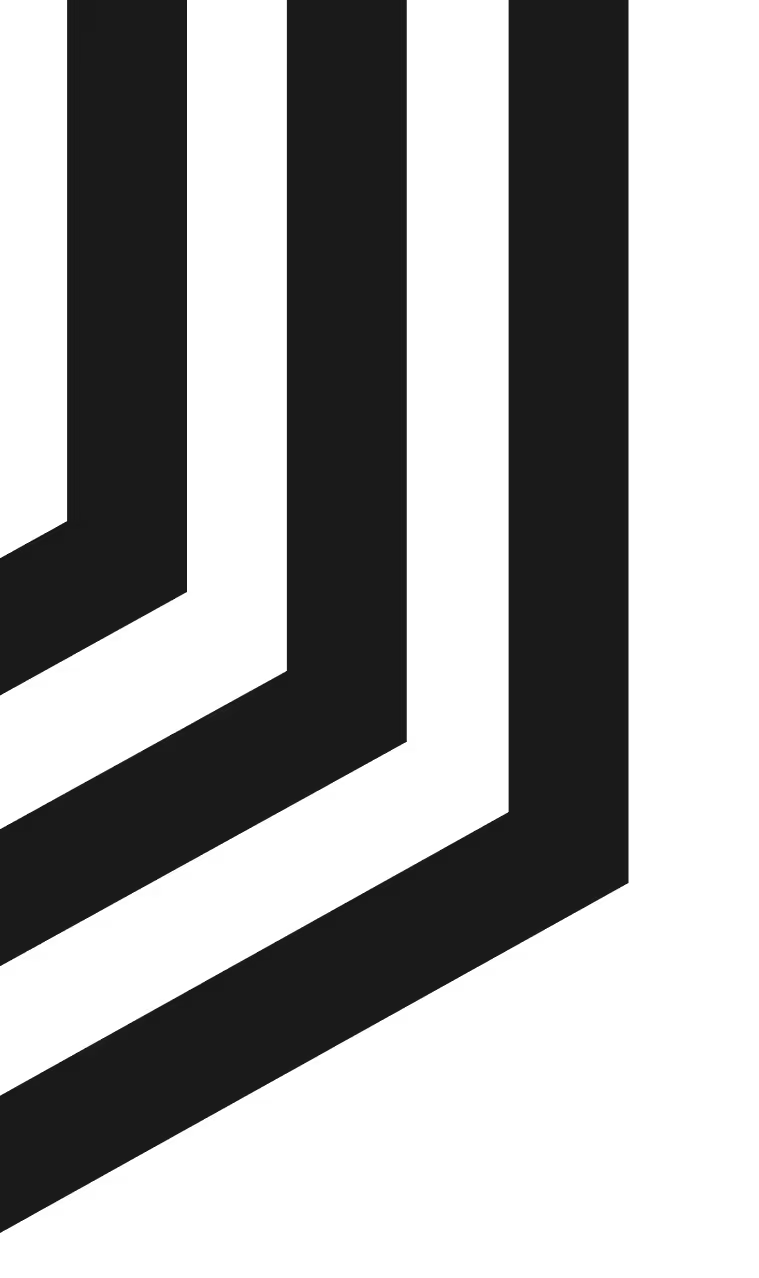