A Novel Approach to Thermographic Images Analysis of Equine Thoracolumbar Region - The Effect of Effort and Riders Body Weight on Structural Image Complexity
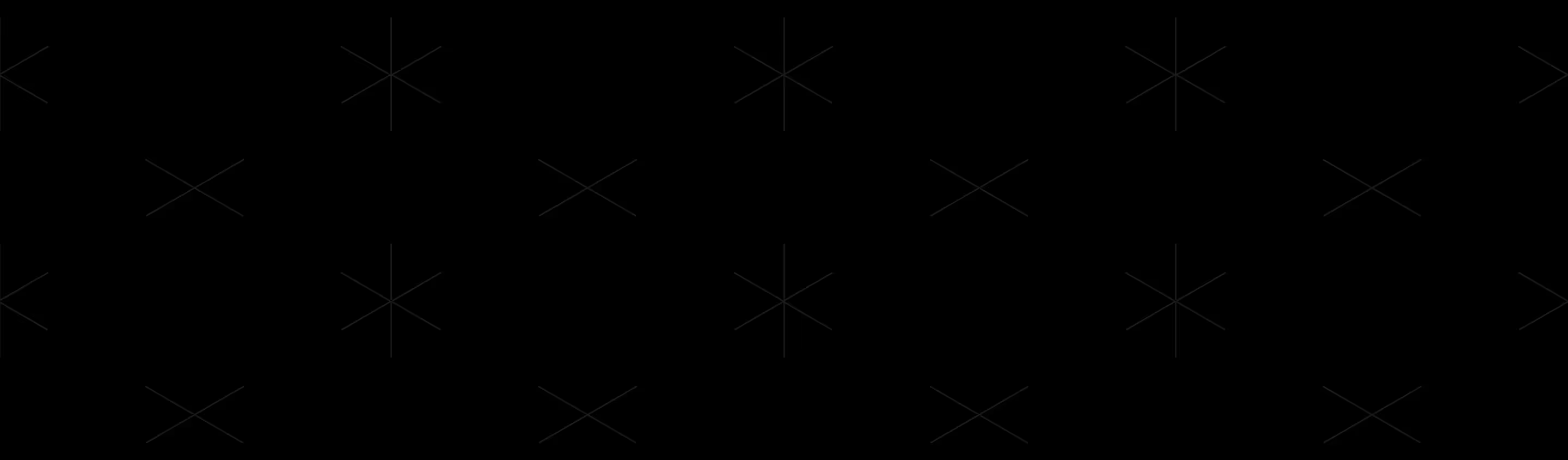
Abstract: The horses' backs are particularly exposed to overload and injuries due to direct contact with the saddle and the influence of e.g. the rider's body weight. The maximal load for a horse's back during riding has been suggested not to exceed 20% of the horses' body weight. The common prevalence of back problems in riding horses prompted the popularization of thermography of the thoracolumbar region. However, the analysis methods of thermographic images used so far do not distinguish loaded horses with body weight varying between 10 and 20%.
Results: The superficial body temperature (SBT) of the thoracolumbar region of the horse's back was imaged using a non-contact thermographic camera before and after riding under riders with LBW (low body weight, 10%) and HBW (high body weight, 15%). Images were analyzed using six methods: five recent SBT analyses and the novel approach based on Gray Level Co-Occurrence Matrix (GLCM) and Gray Level Run Length Matrix (GLRLM). Temperatures of the horse's thoracolumbar region were higher (p < 0.0001) after then before the training, and did not differ depending on the rider's body weight (p > 0.05), regardless of used SBT analysis method. Effort-dependent differences (p < 0.05) were noted for six features of GLCM and GLRLM analysis. The values of selected GLCM and GLRLM features also differed (p < 0.05) between the LBW and HBW groups.
Conclusion: The GLCM and GLRLM analyses allowed the differentiation of horses subjected to a load of 10 and 15% of their body weights while horseback riding in contrast to the previously used SBT analysis methods. Both types of analyzing methods allow to differentiation thermal images obtained before and after riding. The textural analysis, including selected features of GLCM or GLRLM, seems to be promising tools in considering the quantitative assessment of thermographic images of horses' thoracolumbar region.
Reference:Â Malgorzata Masko, Marta Borowska, Malgorzata Domino, Tomasz Jasinski, Lukasz Zdrojkowski, Zdzislaw Gajewski. (2021) BMC Vet Res Mar 2;17(1):99.
Interested in learning more about thermal imaging? Request a demonstration with Digatherm and discover how veterinary thermography can help you find problem areas faster and easily monitor treatment progress.
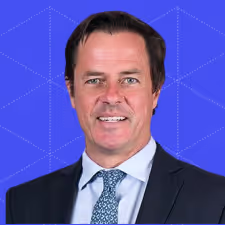
Chief Commercial Officer at Multisensor AI (NASDAQ: MSAI), I help industries prevent equipment failures with AI-powered condition-based monitoring, drawing on 30+ years in investment, private equity, and consulting.
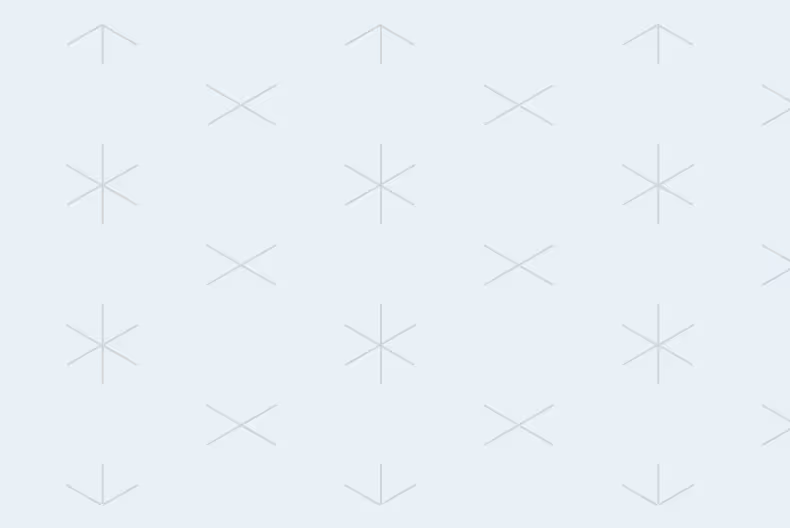
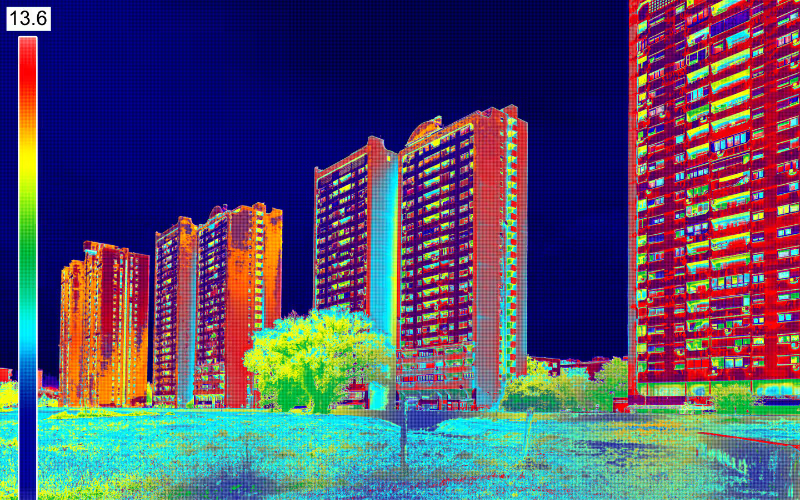
The world around us is filled with hidden information, which can often be revealed by temperature variations that are invisible to the naked eye. Thermal imaging technology steps in, acting as a powerful tool to reveal these anomalies. By translating heat signatures into visual images and providing precise temperature value readings, thermal cameras offer a unique perspective, uncovering a wide range of issues across various industries. In this blog post, we'll delve into some of the most common problems that can be identified using thermal imaging technology.
Optimizing Industrial Processes Â
In the industrial sector, thermal imaging plays a vital role in optimizing processes and ensuring smooth operations. Thermal cameras can identify overheating components in machines before they fail, allowing for predictive maintenance and avoiding costly breakdowns. This is particularly valuable in production lines, where stopping a machine can significantly disrupt operations and impact production targets. In addition to supporting machinery health, thermal imaging can reveal uneven temperature patterns in industrial processes, helping to identify inefficiencies and optimize production.
Keeping Buildings Safe and Efficient
Thermal imaging plays a crucial role in ensuring the safety and efficiency of our buildings. It excels at pinpointing electrical faults, such as loose or corroded connections, overloaded circuits, and overheating componentsâall of which are potential fire hazards. Detecting these issues early allows for timely repairs that can prevent costly damage and ensure the safety of the buildingâs occupants.
Thermal cameras can also expose issues and anomalies in a building's envelopeâthe physical barrier between the conditioned interior and the outside environment. As one example, this can help identify areas where heating or cooling energy is escaping through inadequate insulation. By revealing these hidden inefficiencies, thermal imaging empowers building owners and managers to take corrective actions to increase energy efficiency and lower utility bills. Additionally, hidden leaks in plumbing systems can cause significant water damage and pose health risks. Thermal imaging's ability to detect the temperature difference between wet and dry areas proves invaluable in locating leaks behind walls, floors, or even underground.
Thermal Imaging: A Powerful Tool for Diverse Industries
The applications of thermal imaging extend far beyond traditional industries. Here are a few additional areas where this technology offers significant benefits:
- Predictive maintenance in renewable energy: Thermal cameras can be used to inspect solar panels for defects or hotspots that could impact efficiency. Similarly, they can identify potential issues in wind turbines, allowing for proactive maintenance and ensuring optimal energy production.
- Quality control in manufacturing: Thermal cameras can be used to identify defects in products during the manufacturing process. For instance, they can detect inconsistencies in temperature distribution on castings, potentially revealing flaws that would otherwise go unnoticed until later stages and require costly rework.
- Data center efficiency: Thermal imaging can be a valuable tool in data centers, helping identify hotspots in servers and other equipment. By proactively addressing these issues, data center operators can ensure optimal performance and minimize energy consumption.
- Facility management: Thermal imaging can be a valuable tool for facility managers, helping them identify potential problems with HVAC systems, locate missing insulation in pipes, and even detect rodent activity within buildings.
Quality Control with Thermal Imaging
Thermal imaging has become an indispensable tool for ensuring product quality and process consistency in manufacturing environments susceptible to temperature variations. Unlike traditional inspection methods that rely on visual cues or physical contact, thermal imaging offers a non-destructive and quantitative approach to quality control.
By capturing and analyzing thermal signatures, manufacturers gain valuable insights into temperature distributions across their products and processes. This enables them to:
- Verify product quality: Thermal imaging can detect even minute temperature variations that might indicate defects related to uneven heating or cooling. This allows manufacturers to ensure their products meet specific temperature requirements and avoid potential failures.
- Enhance process consistency: Thermal cameras can reveal subtle variations in temperature patterns across a production line. These variations might signal inconsistencies in the manufacturing process, such as improper heating or cooling settings. By identifying these inconsistencies early on, manufacturers can take corrective actions to reduce defects and minimize waste.Â
Inspection Services
To fully harness the potential of thermal imaging, consider hiring qualified and trained professionals to perform inspection services. MSAI Inspection Services offers expertise in leveraging thermal imaging technology to identify potential issues and optimize operations.
Professional inspection services enhance asset reliability by helping detect problems early, allowing for preventive maintenance and reducing unexpected failures. These services also help ensure compliance with industry regulations, avoiding penalties and maintaining certifications. Additionally, inspections boost energy efficiency and support data-driven decision-making through detailed analyses, optimizing maintenance and investment strategies.
The Future of Thermal Imaging
As thermal imaging technology continues to evolve, we can expect even more innovative applications to emerge. Integration with artificial intelligence and advanced data analysis will unlock new possibilities for preventive maintenance, remote monitoring, and process optimization across a vast array of industries.Â
Here at MultiSensor AI (MSAI), our cloud-based solutions harness the power of thermal imaging alongside advanced sensor data and AI analysis to create comprehensive solutions. MSAI Connect empowers users with real-time insights, enabling them to proactively address potential issues and optimize operations.
Thermal imaging is a powerful tool with immense potential. By leveraging this technology alongside other advanced sensors and AI analysis, even more comprehensive solutions can be created for a wide range of challenges. Explore our blog to learn more about how AI-powered thermal imaging solutions can help you see the unseen and achieve new levels of efficiency and safety.
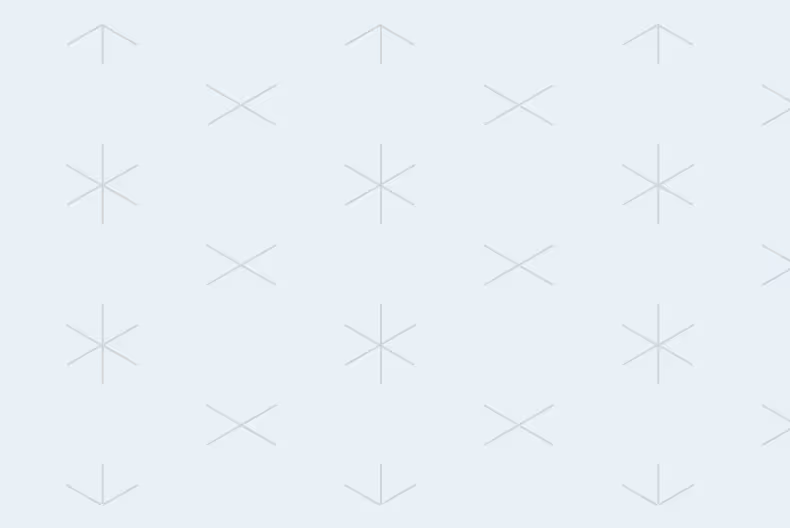
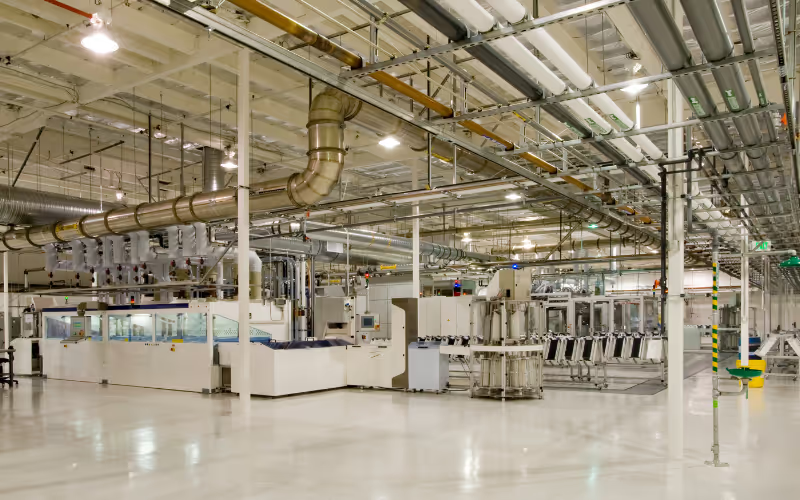
Proactive equipment maintenance is important for businesses of all kinds, but itâs especially critical in industries like manufacturing, distribution, and electrical power production, which depend on seamless equipment operation. Proactive maintenance takes different forms, with some more effective than others. Prescriptive maintenance (RxM) is at the forefront of proactive asset management, providing more actionable insights than previously possible. An RxM program not only alerts reliability professionals to potential problems but also provides specific information on the type of problem thatâs arising and what actions are required to address it.
How is prescriptive maintenance different?
You can think of proactive maintenance as a continuum of methods that provide various degrees of insight into equipment needs. Which method is ideal for any particular business depends on several factors. A company with more critical and valuable equipment will benefit more from prescriptive maintenance, and one that already has equipment monitoring and data management infrastructure in place will be better prepared to implement such a program. On the other hand, companies with less critical or costly equipment may be well served by a less robust maintenance plan.Â
Scheduled Preventive Maintenance
At one end of the spectrum is calendar based preventive maintenance. In its most basic form, this relies on equipment manufacturersâ recommendations to create a regular schedule of maintenance tasks. It doesnât require any special technology and is generally more cost effective than simply letting equipment run until it fails. For small businesses, businesses with low equipment costs, and those that can better accommodate downtime, this can be an advantageous method.Â
Even when rigorously following a preventive maintenance pre-planned schedule, problems can arise unexpectedly. When they occur between scheduled maintenance events, unplanned downtime and potentially costly repairs can follow. On the other hand, because it lacks insight into how machinery is actually functioning, simply following a maintenance schedule can also involve some degree of waste.
Additionally, following a scheduled preventive maintenance process can potentially introduce problems where none previously existed. For example, a large gear box, when new, is essentially a sealed system. However if the manufacturerâs preventive maintenance schedule calls for opening and visually inspecting the gear mesh, then the maintainer would need to open the casing, exposing the interior workings of the gear box to contamination and thereby introducing a failure mode that hadnât existed prior to this visual inspection.Â
Condition-Based MaintenanceÂ
A condition-based maintenance strategy utilizes real-time data input from sensors. Alerts and notifications are triggered when the sensors detect a need for maintenance based on preset thresholds for operational variables like temperature, vibration, and energy usage. (This is true for MSAI Connect, a fixed mounted continuous monitoring solution, but we should also mention route-based inspections. People can have an in-house team or hire an inspection service company to perform these⊠we should emphasize hiring experienced professionals. Inspections should be performed by experienced experts leveraging cutting-edge technologies. Inspection helps to ensure efficiency and reliability in their operations. Plus, they help ensure compliance.) When a sensor detects an anomaly, workers can be instantly alerted so they can take immediate action to investigate the issue. This not only helps safeguard valuable equipment but can also protect public and worker safety by detecting leaks and electrical hotspots as soon as they occur.(CbM can also identify mechanical inefficiencies, i.e. a failing bearing or overtightened conveyor belt.)Â
Predictive Maintenance
Predictive maintenance uses a combination of sensors and data analytics to identify trends and predict when a machine is likely to fail. Because it uses data-driven insights in addition to real-time operational data, a predictive maintenance system can detect problems earlier than condition-based monitoring alone. This allows businesses to schedule maintenance when itâs needed while reducing unplanned downtime.
Prescriptive Maintenance
Prescriptive maintenance is the next generation of proactive equipment maintenance. It does everything a preventive maintenance system does and adds the power of AI and machine learning to take the next steps of pinpointing the root causes of issues and recommending specific solutions. Instead of simply giving a heads up that thereâs a problem with a particular machine, a prescriptive maintenance system can identify the root cause of the issue and provide insight as to how to prevent it in the future. For example, the system might recommend specific maintenance task, or specific setting adjustments, to optimize asset performance and prevent unexpected failure.
MultiSensor AI for RxM
MultiSensor AI is at the forefront of developing technologies that make prescriptive maintenance possible. The MSAI Connect platform is a prime example. MSAI Connect combines advanced sensing and imaging technologies that capture a wide range of data on equipment health with AI-powered software that analyzes this data to identify patterns, predict potential problems, and deliver prescriptive recommendations to optimize machine performance and prevent failures. An RxM program backed by MultiSensor AI can help equipment-reliant businesses minimize downtime, make better informed decisions about equipment care and upkeep, and reduce equipment maintenance and replacement costs.
All businesses can benefit from a proactive approach to equipment maintenance. While a simple routine maintenance plan may be the right solution for many companies, those that depend heavily on the seamless operation of high value equipment need a more robust solution. MultiSensor AI provides the cutting-edge tools these businesses need to implement condition-based, predictive, or prescriptive maintenance programs. Browse our blog to learn more about how to build a more effective maintenance strategy.
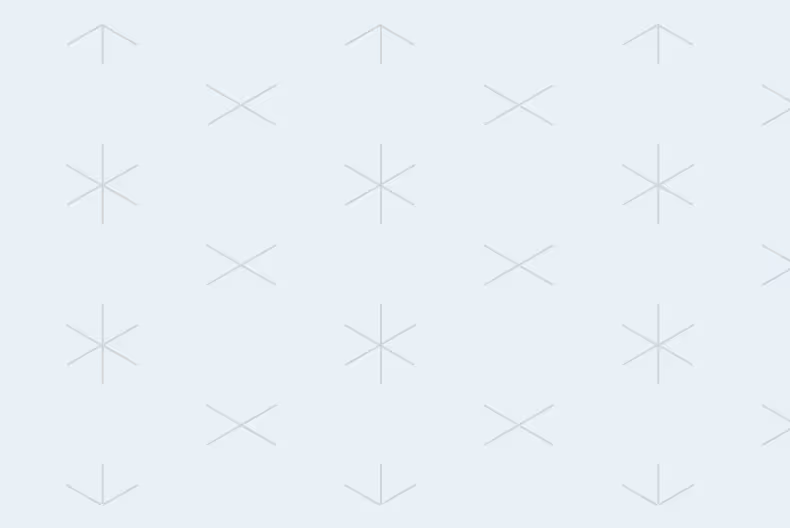
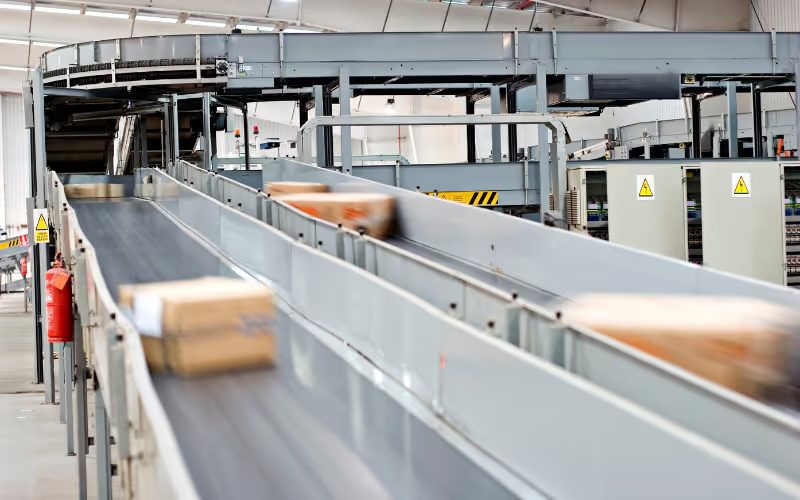
If you depend on machinery to keep your operation running smoothly, how you manage your companyâs equipment is vitally important. There are two main approaches to maintaining these critical assets: run to failure (RTF) and condition-based monitoring. In this article, weâll explore the benefits and drawbacks of each approach and discuss how you can optimize the health of your companyâs assets.
Run to Failure
RTF is a reactive maintenance strategy. You allow equipment to run until it stops working. This âif it ainât broke, donât fix itâ strategy can be tempting to adopt because it allows you to keep everything moving as long as possible, avoiding the need to invest in monitoring equipment or interrupt progress with planned downtime. Rather than spending resources on proactive maintenance, you focus that energy on productivity.
RTF, however, can be a risky approach. When you allow equipment to keep running until you encounter a problem, downtime becomes unpredictable, repairs are often more costly, and malfunctioning machinery is more likely to pose safety hazards to employees and perhaps even the larger community. When breakdowns occur, the costs associated with these issues can quickly surpass the time and money you save in the short term.
Condition-Based Monitoring
CBM, on the other hand, is a proactive strategy for asset management. Using sensors and advanced data analytics, businesses can detect issues at their earliest stages, before they escalate into larger problems, significantly disrupt operations, or threaten worker health and safety. When properly implemented, CBM saves time and money while enhancing worker safety.
CBM vs. Preventive Maintenance
CBM is not the old preventive maintenance model. In the past, a proactive approach to equipment maintenance required regularly scheduled maintenance aimed at preventing problems from occurring. Parts were replaced according to manufacturersâ recommendations, no matter their actual condition, to head off issues. While this can reduce risk compared to an RTF model, it tends to both waste resources by fixing nonexistent problems and miss issues that arise between regularly scheduled maintenance tasks. By utilizing sensors and AI-enabled data analysis, managers get real-time insight into the condition of machinery and components, allowing them to target maintenance where itâs needed most without having to wait for problems to surface.
Benefits of Condition-Based Monitoring
CBM offers businesses multiple benefits, including the ability to perform predictive maintenance, extend equipment life, save time and money, and improve safety.
Predictive Maintenance
Predictive maintenance is an asset management strategy that uses the power of AI to glean actionable insights from sensor data. Sensors collect data on variables like temperature and vibration, which remain within a certain range during normal operation. Changes in these variables often indicate specific changes in how a machine is operating. Users set key performance indicators for each machine, and the AI analyzes the constant stream of sensor data, allowing key employees to view detailed customized reports via a single pane of glass. Instant notifications can alert decision-makers to anomalies, so they can order appropriate maintenance precisely when and where itâs needed. This allows businesses to save money in multiple ways.
- Catching problems early can prolong equipment life, increasing the ROI of these assets.
- A predictive maintenance program can reduce maintenance costs by eliminating the need for regularly scheduled tasks.
- When maintenance isnât an emergency, managers can schedule tasks for when downtime will have the least possible impact on the operation.
Customer Satisfaction
When your operation runs smoothly, your business is best able to keep your customers happy and coming back to you. Preventing equipment failure allows you to consistently deliver products on time. Not only does this help your business grow, but it also prevents costs associated with customer dissatisfaction such as refunds, contractual penalties, customer attrition, or even lawsuits.
Workplace Safety
Real-time alerts help ensure that equipment problems donât slip through the cracks due to improper maintenance practices. Because properly running equipment is less likely to injure workers or cause any kind of environmental or property damage, condition-based monitoring can be an integral part of an overall risk management strategy. Additionally, when you invest in building a safer workplace, you help build a more satisfied workforce. In turn, you can enjoy lower turnover rates and reduce overall hiring costs.
An RTF approach to asset maintenance may save time and money in the short term, but it poses significant risks to profitability as well as workplace safety. Condition-based monitoring allows businesses to avoid unnecessary routine maintenance costs without risking costly and potentially dangerous equipment failures. With continuous monitoring and real-time insights into equipment operation, organizations gain greater control of their critical assets.
MultiSensor AI for Effective CBM Implementation
MultiSensor AI (MSAI) is an AI-powered condition monitoring system designed for industrial environments. Easily integrable with common business intelligence systems like EAM, DCS, PLC, and SCADA, MSAI can automatically generate work orders or trigger other responses to anomalies in the system you already use. To provide businesses the security and accessibility features that best support their specific needs, MSAI is available for both cloud and on-premises use.
To learn more about condition-based monitoring, predictive maintenance, and how AI can power more efficient and effective asset management, browse the MSAI blog.